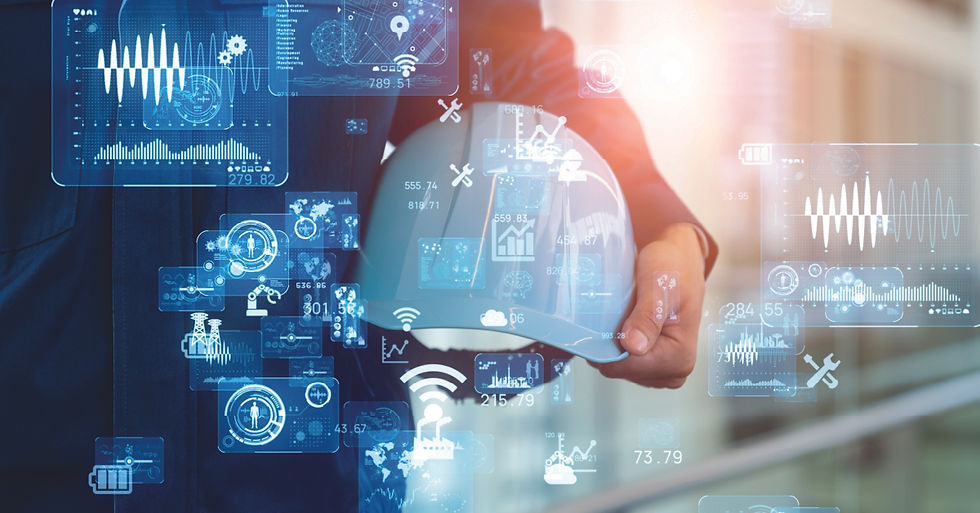
Businesses across industries lost an approximate $7.8 billion due to bad financial data in 2021. This is no small amount, and it can be difficult to understand how it applies to your organization. This number is even more impossible to ignore if you are working in the construction industry, given the cost of bad construction data. In 2020 alone, contractors lost an approximate $1.8 trillion to bad construction data, which in turn prevents ad hoc analysis and impedes growth.
Bad data is defined by inaccuracies, incompletions, and/or inaccessible information collected that simply isn’t doing you any good. If you’ve got some, you’re in good company. Thus, in instances where you ordered excessive supplies for a project, overbid on a job, etc, it likely wasn’t you. It was your data.
Such findings come from a survey conducted by FMI Corporation and Autodesk, which also found that almost 1 in 3 respondents felt they were receiving poor data, which was in numerous cases resulting in bad decisions and stymieing ad hoc analysis efforts. This blog will dive into how you can trace the root cause of your data inaccuracies, what actions you can take to improve your data and how that will positively affect your worksites, and what new technologies can maximize your data insights and efficiency.
Understanding the Source of Bad Data
The first step in fixing your data problems is examining some of the sources of the poor information you’re getting. Most organizations have some sort of method in place for collecting information from job sites. You may have paper forms, emails, scheduled meetings, and text messages flying back and forth, that connect the office and the site to at least some degree. If there’s a gap in the initial plan, however, these communication techniques may ultimately fail.
The problem is primarily rooted in the inconsistency and disorganization in these methods, which can hinder efforts to pivot direction in a crisis or get you through disputes. The following lists out the pros and cons of various methods your organization likely uses:
1. Spreadsheets
Spreadsheets are pervasive in construction, in addition to finance functions across industries. For several decades, Excel was regarded as the peak resource for data collection and storage for good reasons. With 1.8 billion users worldwide, it is consistently universal, and offers useful visualization and data insights. However, this perennial application can result in costly mistakes despite its numerous advantages.
A single spreadsheet can have formulas numbering in the thousands, any one of which could contain errors that misrepresent the data. Company owners are often shocked to discover how inaccurate their spreadsheets truly are; the same sheets they’ve been using as a foundation for making huge corporate decisions and on which they base their bids.
Many point out how Excel can be emailed around with ease. But with everybody passing around versions of a spreadsheet, it is nearly impossible to truly tell if you’re dealing with the latest and most accurate data. This issue becomes even more complicated when you try to keep the information secure across transfers.

2. Pen and Paper
Paper records of events can be an invaluable tool for collecting information, but it suffers some major pitfalls. The first lies in the collection itself. Forms that are half-filled contain only half of the required information. Words may be mixed up, numbers may be smudged, and names may be misspelled, all of which prevent an organization from drilling down to the truth during an ad hoc analysis, to come up with the answers it needs. Papers get wet, dirty, and eventually, some get lost, rendering them completely useless in the future.
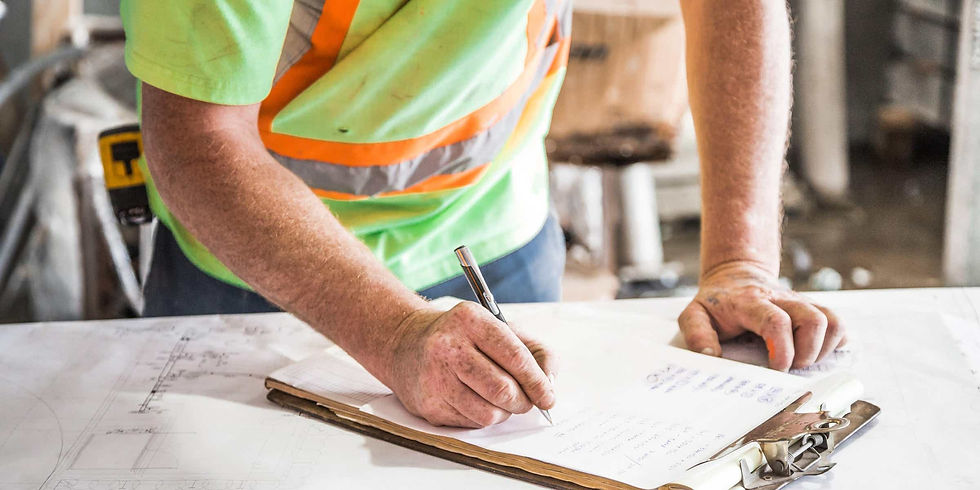
This brings us to the second downside of paper: its organization. How many times have you found old notes stuck between the truck seats? Missing documentation does not help back up your version of events in difficult circumstances like legal disputes. Unless the papers are meticulously organized and thorough, paper notes are largely inadequate for tracking jobsite occurrences.
Even meticulously collected and filed paper notes lack share-ability. How is paper information disseminated around the company? Managers often do not get paper updates about site activities until their weekly meetings. By the time those 7 days pass, the report may be completely irrelevant. Any time sensitive or site crisis has been handled before managers can get a long view on the situation.
Paper had its time as a data collection tool, but that time has passed.
Moving Forward with Proper Communication & Data Collection
Construction can be a complex industry that requires systematic methods for collecting information on each job, and organizational methods that will make key data easier to find in the future.
The Ramifications of Incomplete Data
You are likely curious about what all this incomplete, hard-to-track, miscalculated information is costing your organization. It may be more than you think. Consider all the times you make gut decisions, on how you’ve always done it, or on the information in your spreadsheets. There’s a chance you could be bidding too high, or too low due to your misinformation. Accurate bids are created using front-to-back knowledge of average administrative, labor, and supplies costs on similar jobs. The best way to gauge these costs is to first recognize projects founded upon key criteria and then to analyze data about them. Without complete and correct information, you may be bidding blind. If you guess or use wrong information to construct your bids, you may be leaving money on the table by bidding too low, or go the other way and lose jobs by bidding too high.
Improving Your Data Efficiency
There are two primary ways to improve your construction profit margins:
Earn more money
Do more with the money you already take home
Thorough project data can open a window onto daily site operations, so that you can recognize and amend inefficiencies. Rework is a classic example: though it’s pervasive throughout the construction industry, its roots lie in bad data – either the wrong information has been passed along, or the correct updates were badly communicated. By finding and eliminating rework, you could do more with less and improve your bottom line.
Reaping Takeaways From Your History
When you can look at projects you’ve done before and figure out how to do the next one better, you can avoid pitfalls, do things better, and could even earn proportionally more cash for your work. Accurate, accessible and easy-to-find data can help you avoid scheduling problems, and pivot workforces during interruptions to actually improve the way your organization works.
How to Fix Incomplete Data
Fortunately, the finance function in the construction industry does not have to continue to suffer the pitfalls of poor data. Current data solutions use a few key strategies to help you get a handle on what’s going on at your work sites.

First, systematic data collection can ensure that consistent metrics are being tracked company-wide, to get the coverage you need and give you a benchmark for comparison. Real-time updates provide a single source of truth for your project, meaning no more working from outdated guidelines or struggling to fill in spreadsheet data immediately prior to meetings. Data integration across the various stages of the construction process can also end data silos; each area of your organization can be educated by prior experiences.
Real World Example of the Power of Software
In mid 2021, Bedrock Quartz Countertops was having difficulty with their reporting capabilities. They had already integrated an ERP system specific to the construction industry, but were not putting out reports at the level they had hoped. Their CFO, Rob Anderson, sought to report their data across teams and departments, in addition to automating the dissemination of the information. After integrating the DataRails FP&A software system, the entire team at BedRock Quartz can now help drive business by seeing the data they have constantly sought, but couldn’t receive, because it was so labor intensive to manually report prior to the adoption of the DataRails solution. The case study for this success story is here.
Using Quality Data to Maximize Your Results
The biggest problem with incomplete data is that it stymies the feedback loop that helps leaders improve their businesses, and their industry as a whole. Through establishing a true and complete picture of the work as it happens, companies may actively get better at what they do, and improve their profit margins in the process. You’ll want to avoid becoming a statistic, you should avoid the rework and stop claiming your portion of the giant losses construction organizations suffer as a result of working from incorrect information.
Yorumlar